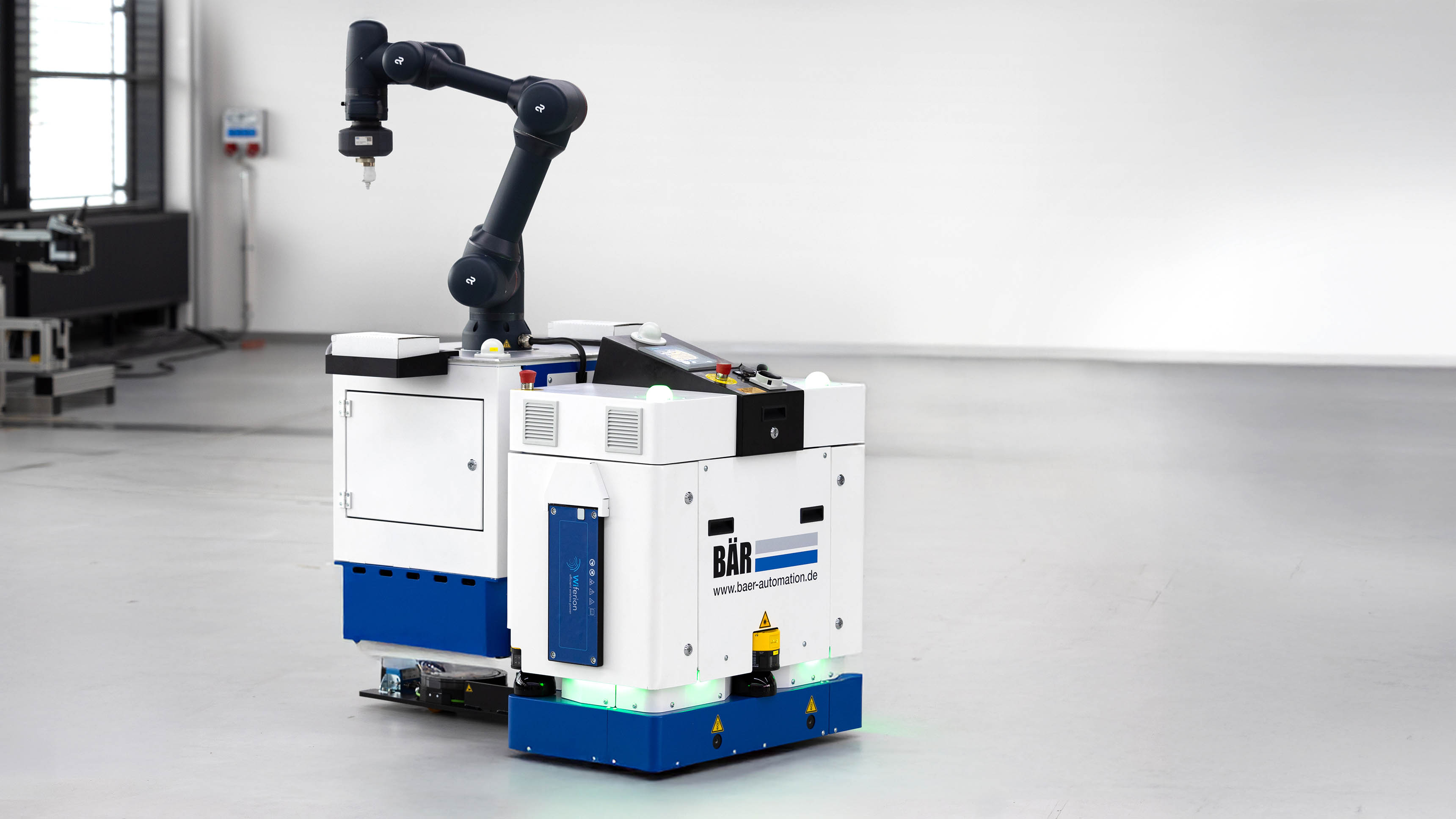
Mobile manipulators: Flexibility through mobility
/ 4 min readMobile robots are now a key element in various factories, responsible for transporting raw materials, moving items between work stations, and delivering finished goods to storage or dispatch areas. These adaptable platforms can carry tools, components, and entire assemblies. When equipped with robotic arms, their potential expands even further. What benefits do these systems provide, and what challenges arise during their integration?
What are mobile manipulators?
A mobile manipulator is a robotic system mounted on a mobile platform, usually an autonomous mobile robot (AMR) or an automated guided vehicle (AGV), which navigates independently using advanced guidance systems, sensors, and cameras. The manipulators are typically lightweight robots, designed to have moderate payload, reach, and precision. Their compact size is crucial since a larger footprint would obstruct the mobile platform's loading area.
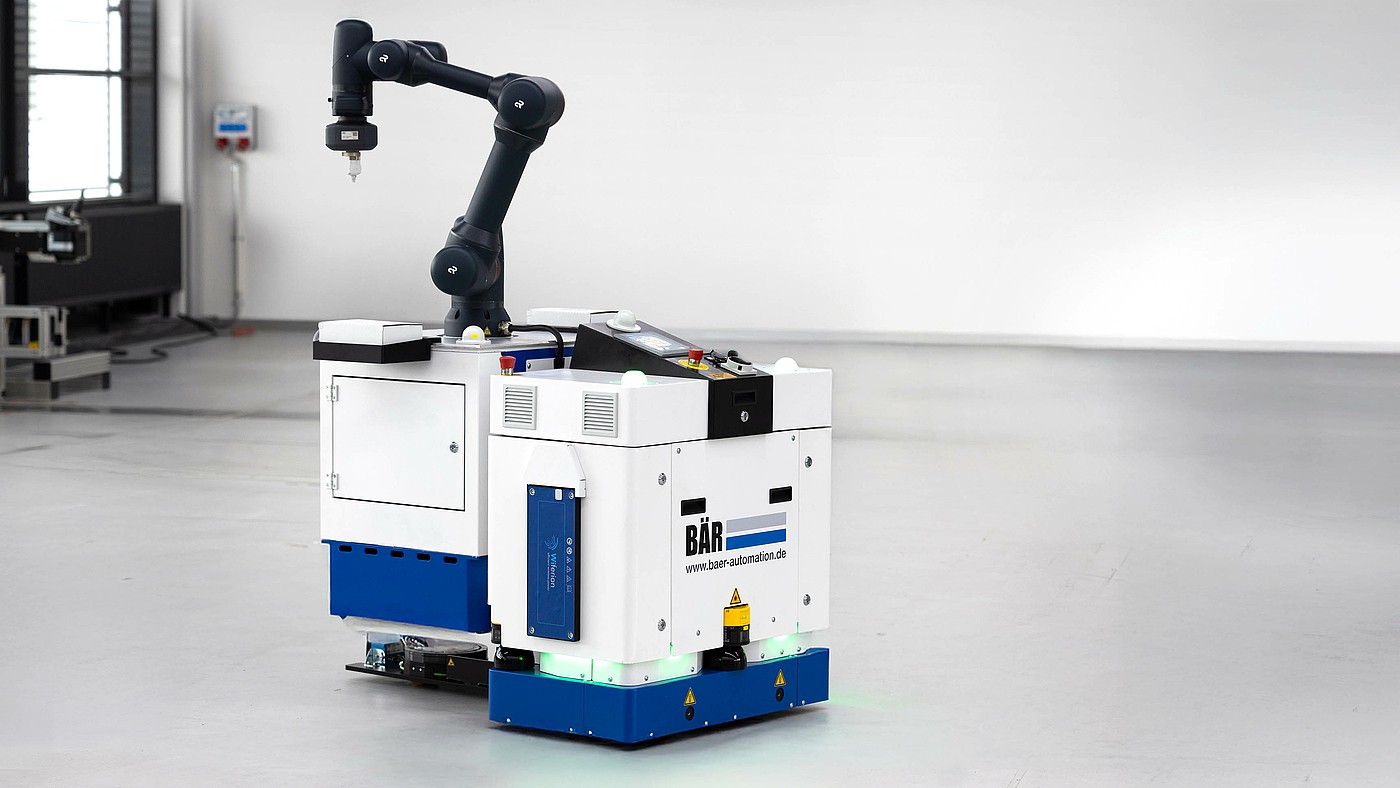
Constraints of AGVs/AMRs & robotic arms
To understand mobile manipulators better, it's important to first explore the limitations of AGVs/AMRs and robotic arms individually. In the real world, robotic arms are typically stationary, mounted next to their designated work areas. This allows for precise operations across a variety of tasks. However, they are inflexible - once placed in a particular location, they can only operate within a defined area and from one direction. If their support is needed elsewhere, they must be dismantled, transported, and reprogrammed.
AGVs/AMRs are mobile and generally do not require rails or predefined routes. They navigate on their own, seek charging stations independently, and avoid obstacles autonomously. However, despite their flexibility in movement, they have two significant limitations: they depend on external loading and can only execute one task at a time, typically transporting goods between locations.
Advantages of mobile manipulators
Mobile manipulators step in where individual components fall short, adding mobility to robotic arms and enabling driverless transport systems to handle their own loading.
This added flexibility extends their range of applications, moving beyond simple material and goods transportation to a broader range of applications and functions.
What advantages does this provide specifically?
1. Quick production adaptation
A shift in demand often calls for product adjustments, or customers may seek alternatives from other suppliers. In traditional production environments, this requires significant changes, often leading to the complete redesign of production lines. This is especially true for traditional conveyor systems like roller conveyors and conveyor belts. Mobile manipulators, however, excel in unstructured settings and can be quickly relocated and repurposed for different tasks, boosting flexibility in production processes.
2. Versatile use
Not all companies can afford to set up complete robotic production lines, so it becomes even more important to ensure that each system is used to its full potential - especially for smaller businesses. A stationary robot that is fixed in place can't be used elsewhere, which is particularly problematic when the robot isn’t running 24/7. This idle time reduces efficiency. Mobile manipulators allow the same robot, previously engaged in e.g. picking, to take on other tasks like quality control, ensuring optimal resource utilization.
3. Enhanced autonomy
AGVs and AMRs usually require external assistance for loading. Typically, they position themselves near a shelf, where an employee manually retrieves parts from boxes and places them onto the loading area. This process can be physically demanding, particularly when heavy lifting or frequent bending is involved. Furthermore, it ties up employees who could be performing more comfortable and value-adding tasks instead. Mobile manipulators eliminate this dependency by autonomously handling order picking and loading, allowing employees to focus on less strenuous activities. This reduces workforce strain and boosts overall productivity.
4. Seamless integration
Every production facility is unique - factors like space constraints, industry requirements, and building design create significant variations. Older factories, originally built for manual labor, often lack the infrastructure for large-scale automation. Mobile manipulators are an ideal solution for these brownfield facilities, as they seamlessly integrate into existing workflows, adapting to their surroundings rather than requiring major structural changes.
Customized solutions
There is a catch to the effective cooperation between robots and automated guided vehicles: If the robotic arm is permanently mounted on the AGV/AMR, it can only be used in combination with the mobile system - and vice versa. The robot permanently occupies the loading area of the AGV. The loading capacity of the mobile system is therefore limited.
Together with BÄR Automation, we developed an innovative solution to this dilemma: decoupling. Instead of permanently mounting the Yu 5 Industrial robotic arm on the AGV, it is installed on a mobile supply station, which contains a charging device and a wireless communication interface. This setup enables independent, battery-powered operation when no charging infrastructure is available. Once the AGV picks up the robot, it charges the robot directly.
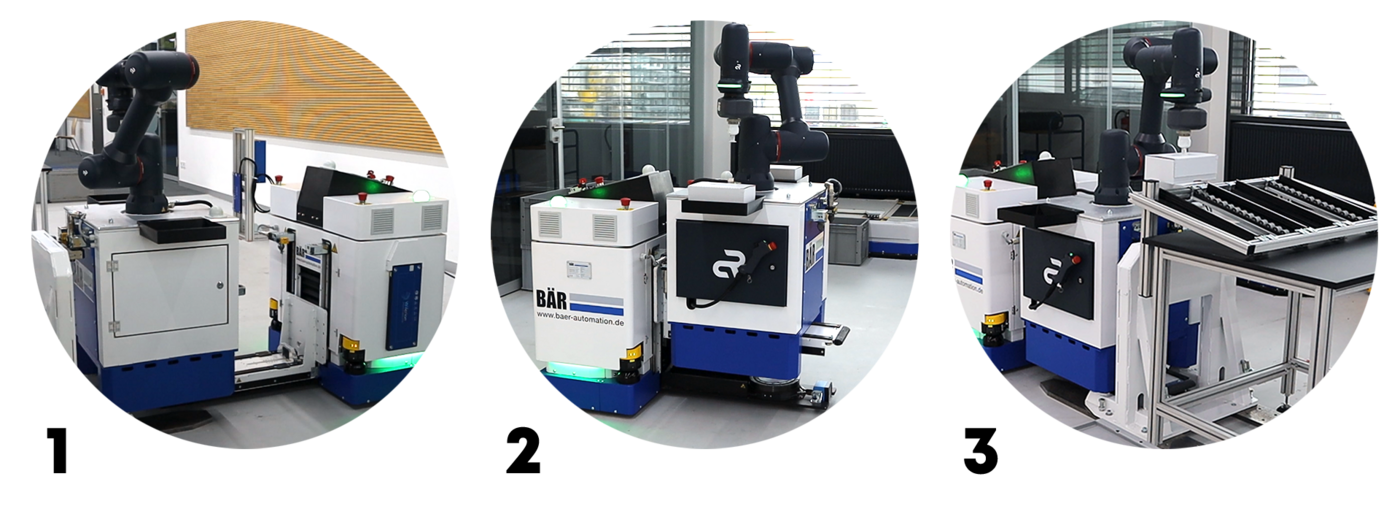
The benefit is clear: while the robotic arm performs tasks at a station, the AGV remains available for material transportation. If the robot is required elsewhere, the AGV momentarily pauses its transport task, lifts the robot, and relocates it. Naturally, the system can also be used as a mobile manipulator when necessary.
These versatile application options form the core of the customized solution known as ConTrax® Robotic System. It gives customers the flexibility to choose how they want to use the individual components, whether independently or in combination, with each approach presenting its own advantages and disadvantages.

With our customized solution, the ConTrax® Robotic System, we can unlock the full potential of both components of the mobile manipulator. Users have the flexibility to operate the AGV and robot arm both modularly and symbiotically, which offers a significant advantage over the rigidly coupled systems typically found on the market
Shared expertise
The ConTrax® Robotic System is a prime example of our cross-company collaboration and holistic approach to automation. At Agile Robots, we don’t just develop cutting-edge, AI-powered robots; we also automate complete production lines, including all the associated components and processes. Together with our partners, we cover the full range of robotics: from advanced, intelligent robotic arms to AGVs, autonomous mobile robots, and AI-driven software.
Efficiency through versatility
Mobile manipulators maximize the benefits of automation solutions. They extend the capabilities of automated guided vehicles and set stationary robot arms in motion. The result is optimal capacity utilization and increased productivity.
This approach benefits not only large corporations but also medium-sized businesses that may not have the resources to invest in large fleets or robot lines. With mobilization, robotic arms can be flexibly deployed at various locations instead of being confined to a single station.
However, as robots and AGVs/AMRs are often interdependent, mobile manipulators have their limitations. Like all automation solutions, each scenario is different and requires careful alignment with the customer’s needs. This is why tailored solutions like the ConTrax® Robotic System are critical and continue to gain importance.
Find out more about our solutions or contact or our experts for a quote.