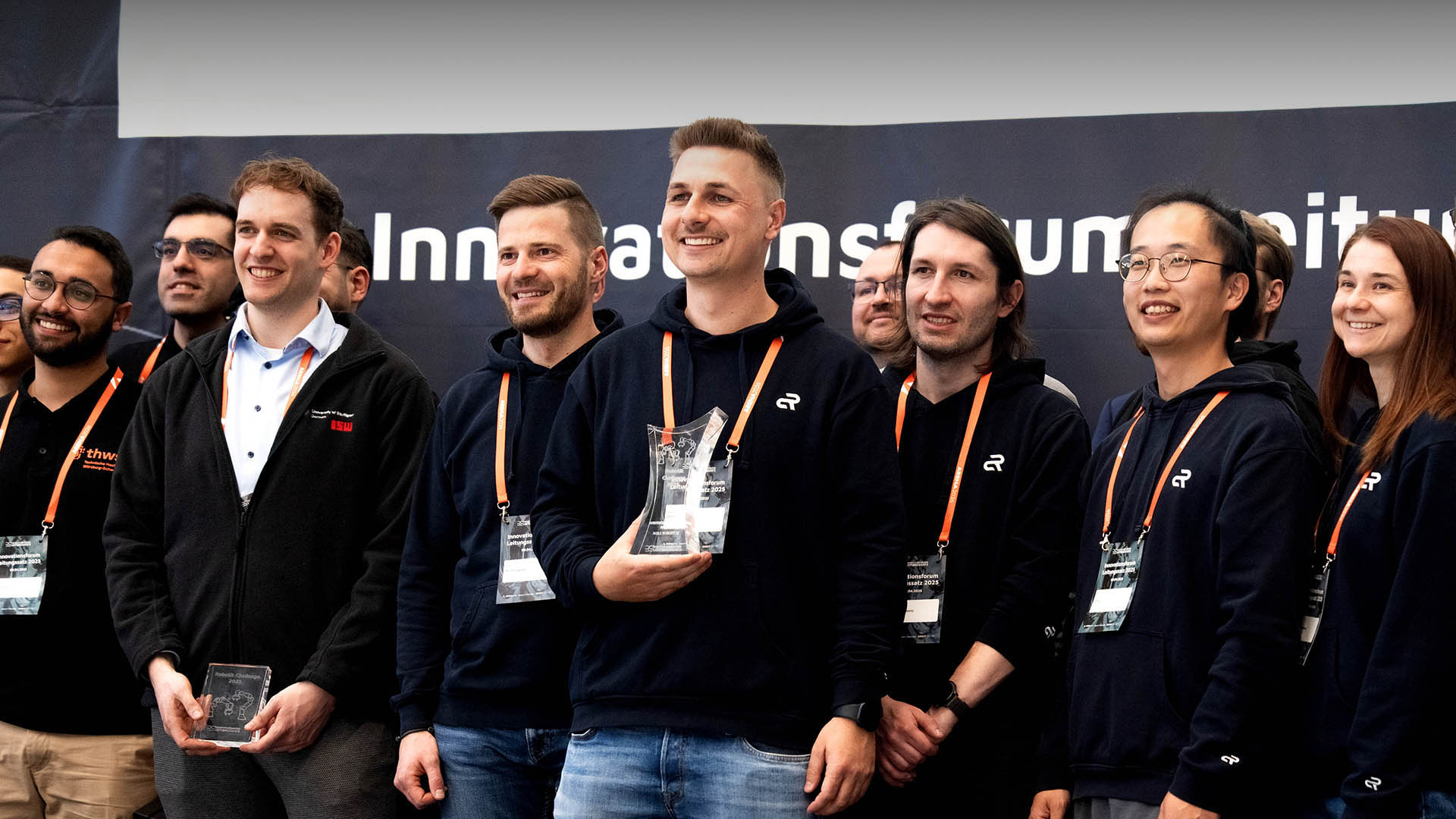
Agile Robots solves Robotik Challenge 2025 the fastest - and wins award for Economic efficiency
/ 3 min readMunich, 10.04.2025 - The leading provider of next-generation automation solutions, Agile Robots, has received an award at the Robotik Challenge 2025 in the Transformation Hub Leitungssatz project at Stuttgart's ARENA2036 research campus. In the “Economic efficiency” category, the Munich-based company impressed with its exceptional cycle time - it was the only team to master the challenge in 2:25 minutes.
Once again, the publicly funded Transformation Hub Leitungssatz project has kicked off the Robotik Challenge this year. Its objective: to automate the production of partial wire harnesses - an area of automotive manufacturing that has seen little automation so far. The primary challenge lies in the complexity of the task, as many robots struggle with the dexterity and precision required to manipulate and position the flexible cables.
The challenge requires inserting five wires, ranging from 0.13 to 1.5 mm² in size, into four different connectors. Key components include Nano MQS contacts (Miniaturized Qualified Connectors), low-profile wires, connectors, and cable ties.
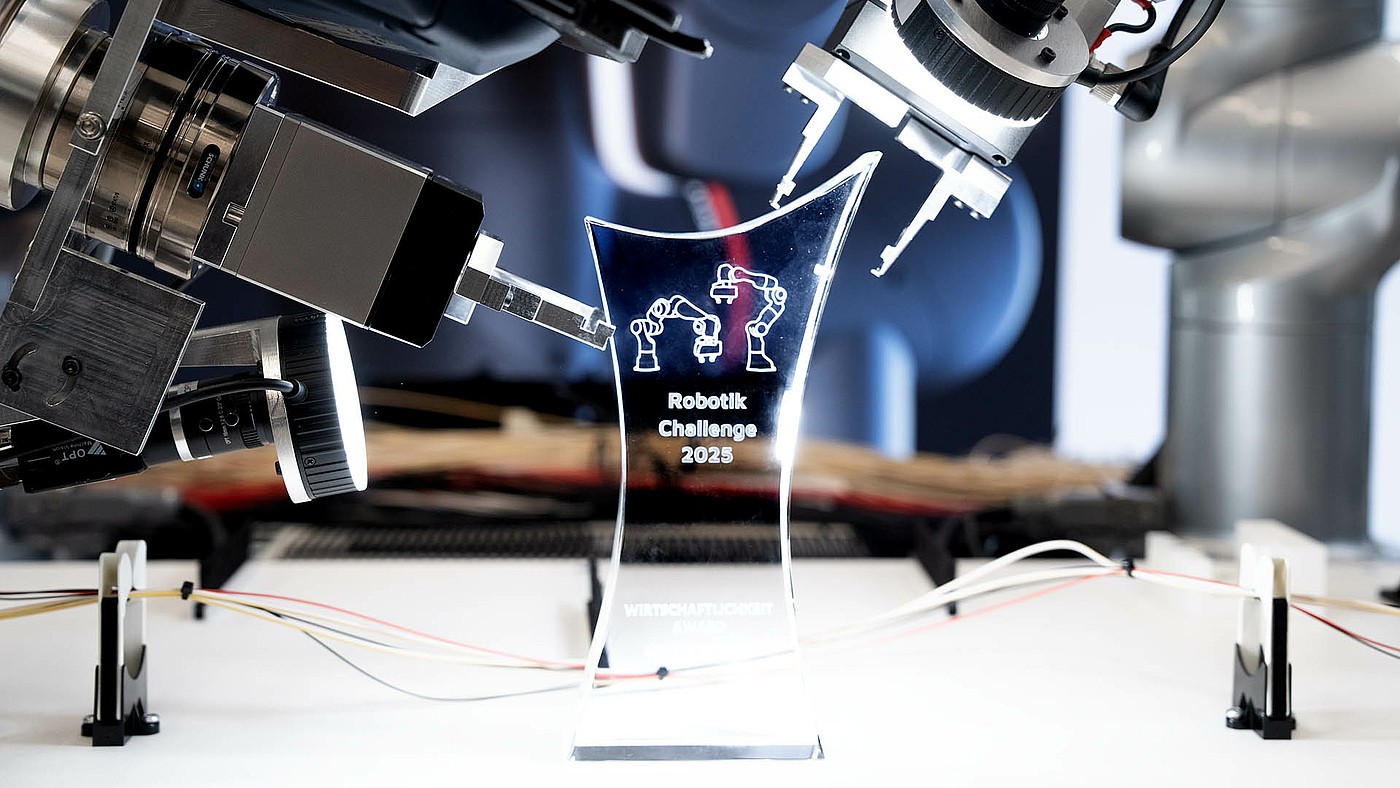
The solution
Right from the planning phase, the emphasis was on practical industrial use. The objective: a fast, precise solution that could be seamlessly integrated into real-world applications.
Therefore, Agile Robots adopted an approach that integrates different technologies and expertise. The hardware setup includes two high-precision, seven-axis Diana 7 robots, two 2D camera systems with ring lights, force-torque sensors, a cable tie tool, and several magnetic closers.
On the software side, the platform AgileCore manages the programming, control, and monitoring of the entire production process. It coordinates robot synchronization, enables integration with external systems, abstracts hardware complexity, and streamlines programming.
Meanwhile, the entire process is enhanced with advanced AI solutions, including intelligent image processing algorithms.
The process
The challenge starts with the Diana 7 robots gripping the cable ends simultaneously and guiding them through the cable fixings. Prior to this, the table on which the fixings are mounted was delivered by the automated guided vehicle ConTrax® Module One from BÄR Automation.
The crimp is then carefully aligned and inserted into the connector with the help of a 2D camera, which is supported by AI-driven image processing algorithms. Meanwhile, the force-torque sensor tracks the forces at play to reduce friction and avoid any potential damage to the crimp. It also verifies the final position of the crimps.
Once the crimps are in place, the secondary locking mechanism automatically closes via a magnetic system. One robot then places the connectors in the housing, and another robot secures five cable ties to the cable harness.
The whole process only takes 2:25 minutes.
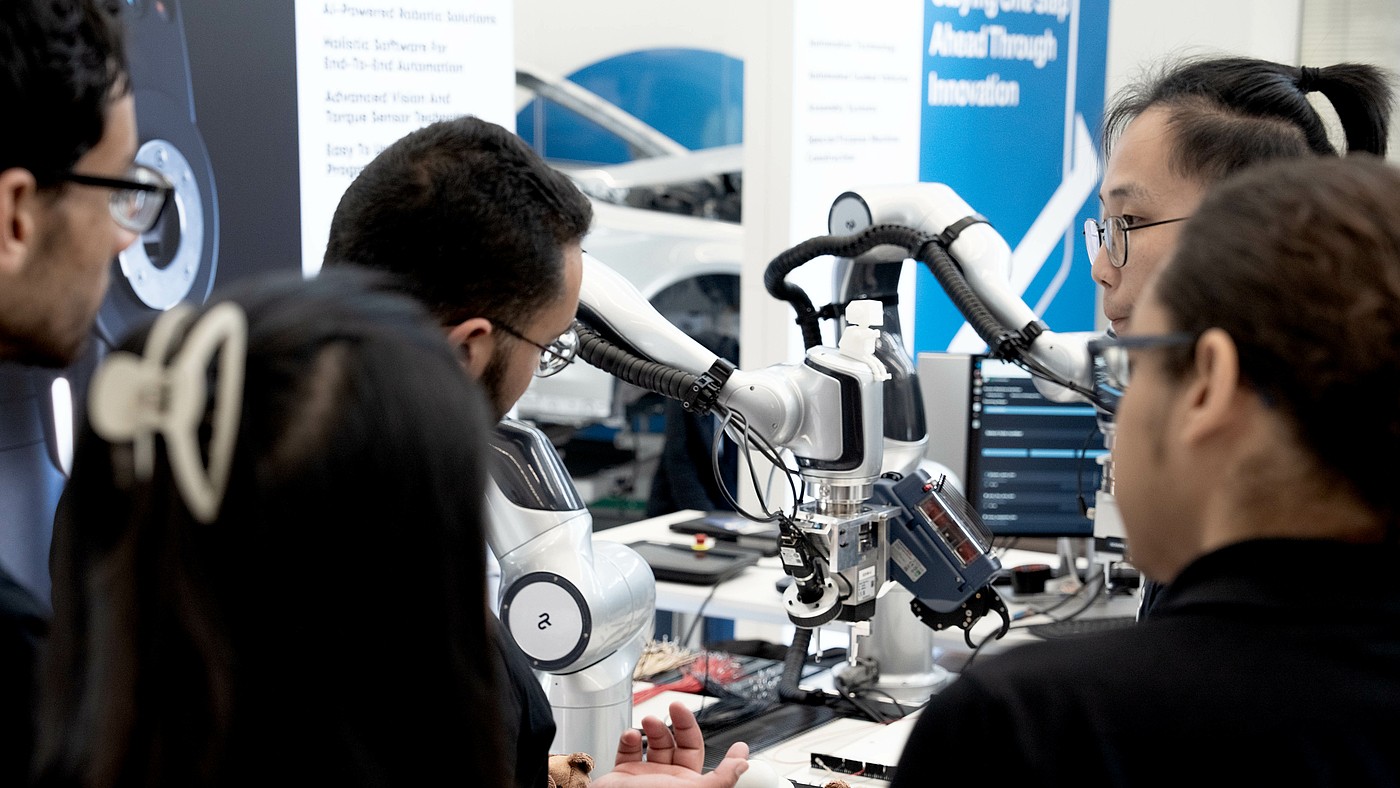
Holistic automation
Agile Robots’ successful solution to the Robotik Challenge marks a significant achievement: the company was the only participant to complete the task well below the target time of three minutes – and did so with remarkable precision.
The award also reflects the company’s successful holistic approach, seamlessly integrating AI, advanced software, and ultra-precise robotic arms to develop customized automation solutions.
Following the success of the Robotik Challenge, Agile Robots now aims to bring these results to the automotive industry and other fields. Several leading cable assembly companies, who witnessed the challenge live at the ARENA2036 research campus in Stuttgart, have already expressed interest.
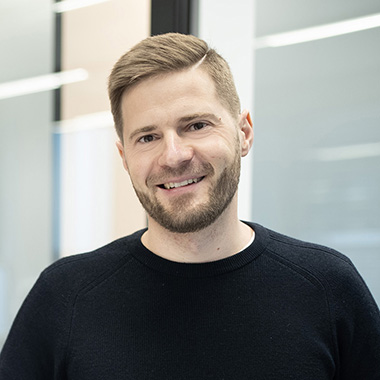
We worked hard, combined different technologies, specialties, and disciplines, and ultimately came out on top. This highlights not only our technical know-how but also the success of our holistic approach to automation.